MedWrench is your online community to ask questions and share information about specific medical equipment you work with every day.


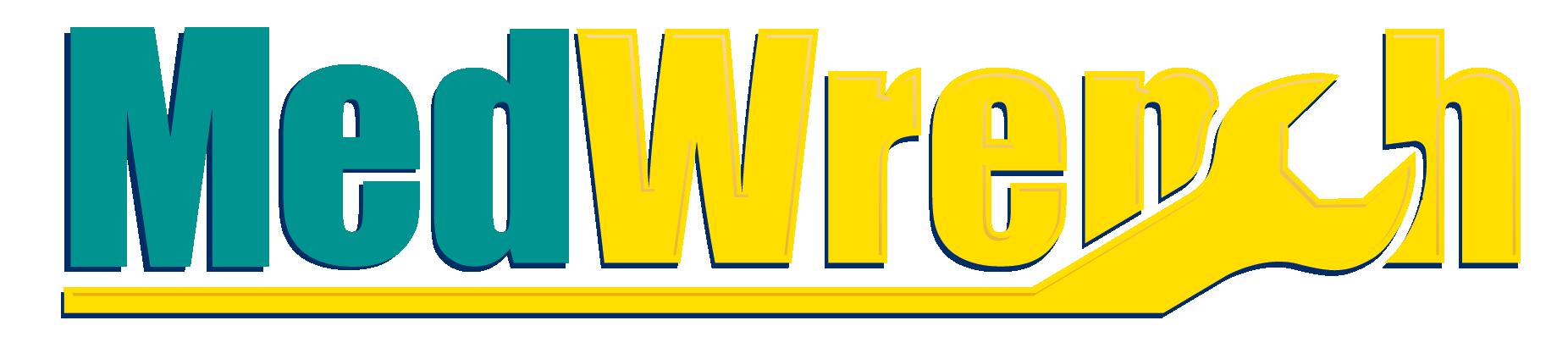
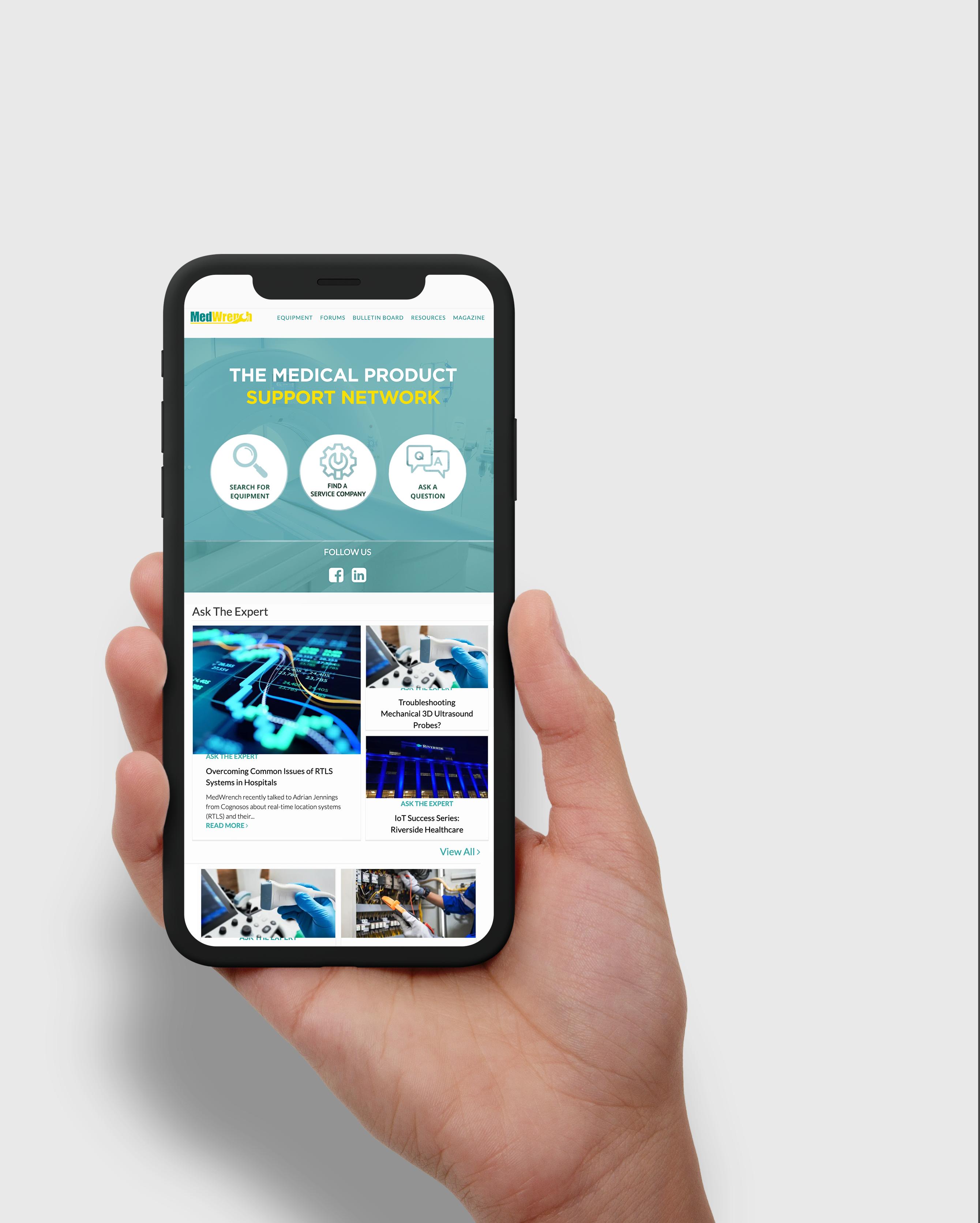
MedWrench is your online community to ask questions and share information about specific medical equipment you work with every day.
Since 2010, the face of MedWrench is Ben Calibrating or Ben C. for short. While he may just be a small Lego figure, you can find him all over the world.
• Is he helping to fix broken equipment at your facility?
• Is he fighting off sharks at the beach?
• Is he crowd surfing at a concert?
The possibilities are endless! How does Ben C. do these amazing things? That’s where you come into play. MedWrench has an ongoing photo contest to see where Ben Calibrating is traveling to and what he has been up to.
Follow MedWrench on Facebook and LinkedIn and checkout the Expos and Events section of the Bulletin Board on MedWrench.com to find us at an upcoming show!
Post your pics with #BenC and tag @MedWrench.
PRESIDENT John M. Krieg
ACCOUNT Starr Smith EXECUTIVE
ART DEPARTMENT Karlee Gower Taylor Hayes Kameryn Johnson
DIGITAL MARKETING Kennedy Krieg Cindy Galindo
ACCOUNTING Diane Costea
ADMINISTRATIVE Joanna Manjarrez ASSISTANT
DATA ENTRY Emma Vitkovitsky
THE FACE OF Ben Calibrating MEDWRENCH
MEDWRENCH is a product focused support network where medical professionals, purchasing administrators, manufacturers, dealers and industry experts can provide opinions, share ideas, and gather relevant information on medical technology and equipment.
Health care providers are challenged with limited capital dollars and shrinking reimbursements. In addition, many are looking at ways to comply with sustainability compliance and doing their part for conserving energy and environmental resources. Maintaining the security of networked medical devices adds an additional burden to an organization’s finances. The r ight to r epair, being the ability for one to repair and maintain items by means other than the original equipment manufacturer, helps provide a practical solution to these challenges.
Are you seeing an increase in the number of products becoming “end of life” or “out of support” even though they are fully functional and meet patient care needs? It seems this is inherent in the design of newer devices to have shorter life cycles, and in turn have continuous revenue. This results in customers being mandated to replace their equipment pre-maturely, in turn incurring a higher capital cost for a health care organization for said replacement, and in many cases, a higher operating cost too due to limitations in support options for the newer devices.
Not all patient care devices may have manufacturer-provided solutions to address operating system obsolescence or other cybersecurity threats, more so when there is already a deflated short support life. When the manufacturer as the only support option states they have no remedy for an issue, considerations for mitigation is sometimes pushed aside and costly replacement is presented as the only solution.
The fabrication of medical devices uses natural resources. The premature disposal of equipment puts a demand upon such resources as not all parts of a device may be recyclable for re-use or environmentally
friendly for its disposal. For most medical equipment, this cost for removal and proper disposal is borne by the health care facility.
Health care providers are caught in a quandary when they have limited options for how to support the medical equipment they own. They have higher operating and capital costs tied to artificially shorter lifespans for items they cannot self-maintain, and are lacking timely access to a trained service provider. If one cannot train their staff or find a qualified alternate service provider, this impacts two critical aspects of a health care organization: providing timely care to the patients it serves and ensuring equipment is being maintained and inspected on schedule.
Cancelled patients means lost revenue, customer dissatisfaction and a physician dissatisfier. Delays in any scheduled preventative maintenance can also increase downtime impact for the health care provider’s regulatory compliance.
A lack of inhouse or aftermarket service options to repair and maintain equipment means that any service-related needs now become a waiting game. Effectively, any planned or scheduled maintenance can only be done only when the manufacturer is available. That may mean cancelling patients during the day when patient volumes are the highest, or by paying a premium for afterhours or weekend
service. Based upon net operating margins of most health care organizations, any premium service costs cut into a health care providers bottom line very quickly and more pronounced than regular service rates.
Many manufacturers are reinforcing their communication to health care providers that non-contract customers come last for response to any service requests. Ironically, several manufacturers are now also extending out their response times for contract customers, too, in light of no longer having external competition. Many have gone from a two-hour onsite response for a full-service contract customer to a four or eight hour onsite response. If one wants the two-hour response, the premium is very costly. For demand service a few manufacturers have extended it out to 24 to 48 hours onsite response. For niche products where the manufacturer offers no training, this is also starting to be seen as the new normal for products under a full-service agreement. This impacts hospitals in their mission of providing timely patient care to those in need and recouping their investment in the equipment.
The lack of right to repair has wide-spread impact. Shrinking revenues means less money to replace capital. Lack of support options for maintaining equipment means items are being replaced at a schedule a
MARK NEWELL Director, Operations Support, Healthcare Technology Management/Clinical Engineeringmanufacturer may dictate, not that of the equipment owner based upon what the owner can afford. Lack of competition, be it through third-party or trained inhouse staff mean higher operating costs and delays in care when something is not available for patient use. Lastly, equipment being replaced prematurely is negatively impacting the environment and related resources to produce that equipment’s replacement.
A long-term holistic solution for medical equipment service is needed for health care facilities to better steward resources and ensure patients get the care they need when they need it. The right to repair helps address these challenges. What one can do to support this is to help get out the message by working with his or her organization’s senior leadership, the organization’s government relations staff and supply chain leaders, insurance providers, and any group purchasing organizations their health care organization may belong to. It comes down to awareness as to how not having options really drives up costs for health care.
“Health care providers are caught in a quandary when they have limited options for how to support the medical equipment they own .”
1 Quality & compatibility
Get access to OEM service parts, accessories, and consumables that are tested for quality and compatibility with your GE Healthcare equipment.
2 Product availability
It’s not just about getting the right parts and accessories. It’s about giving the right care to your patients. When there’s no time for downtime, consider these reasons to order your parts and accessories directly from GE HealthCare:
Order easier and faster with over 85,000 parts and accessories coming from 50+ distributors worldwide with availability verified in real-time.
3 Service & support
Shop parts, accessories, and consumables and schedule repairs online 24/7, or speak to an agent for assistance.
MARCH 6-17
Principles of Servicing Diagnostic X-Ray Systems
Week One eLearning
Week Two on-site at RSTI
MARCH 6-17
PACS Engineering & Administrators Certification
Phase 1
Phase 2
MARCH 15-17
Principles of Servicing Diagnostic Ultrasound Systems
APRIL 24-28
CRES Preparatory Course
MAY 16-18
Introduction to Diagnostic Imaging and PACS for Managers and Sales Professionals
FEBRUARY 20-24
Shimadzu RADspeed
MARCH 6-10
Siemens Ysio
MARCH 20-22
Philips Epiq Ultrasound
MARCH 22-24
Philips iU22/iE33 Ultrasound
MARCH 27-31
Canon RadPRO Digital
Servicing Multivendor Injectors
MARCH 13-24
Philips Brilliance CT
MARCH 20-31
GE non-HD CT Family (Optima, Brivo, VCT, Lightspeed, Brightspeed)
APRIL 3-7
GE Proteus
APRIL 11-21
OEC 9800/9900
Philips Allura Cath Lab
APRIL 17-21
Philips Digital & Bucky Diagnost
Siemens Luminos Agile Hologic Selenia
APRIL 24-28
GE Optima & Brivo Digital Portables
Philips MobileDiagnost Digital Portable
FEBRUARY 27-MARCH 10
GE Excite & GEMS Family MRI
APRIL 24-MAY 5
Servicing Multivendor MRI Systems
MAY 8-19
Siemens Family MRI (Symphony TIMS, Espree, Avanto)
Me dWrench reached out to experienced healthcare technology management (HTM) professionals for an informative look at medical equipment training. Experts participating in this article are Ted Lucidi from Innovatus Imaging and Todd Boyland from RSTI.
1. WHAT TYPE OF TRAINING SHOULD A BIOMED SEEK OUT TO CONTINUE THEIR EDUCATION?
LUCIDI: The answer to this question is based on individual goals. If an individual has a desire to advance into a management role, they should focus on continuing education through a university. Typically, management positions require a 4-year degree, and director-level positions require a master’s degree. For those with little to no desire for corporate or senior roles, continuing education might best be focused on OEM and ISO training opportunities on advanced devices. With the interconnectivity of so many clinical devices, training in IT fundamentals and networking could be highly beneficial.
BOYLAND: Reputable and proven. Training providing an immediate value-add for themselves as well as the employer, allowing an opportunity for the biomed to advance their career.
2. WHAT EDUCATION/TRAINING SHOULD AN ENTRY-LEVEL BIOMED OBTAIN BEFORE SEEKING A JOB?
LUCIDI: There is a wide variety of educational options available for today’s biomed candidates. Some programs span 4-years, others 2, and the most recent is AAMI’s BMET Apprenticeship program. In my opinion, a 2-year program is more than sufficient for entry-level biomeds. The majority of a biomed’s technical knowledge is obtained on-the-job and through specific device trainings via OEMs and ISOs. A potential path could be to acquire an initial education, enter the field, and take advantage of employer tuition reimbursement programs if interested in continuing formal education to further advancement. More than training and education, what is needed, initially, is drive and passion for technology and service.
BOYLAND: A biomed should understand basic electronics and computer networking skills as an entry-level biomed.
3. HOW CAN A NEW BIOMED EARN EXPERIENCE IN THE FIELD?
LUCIDI: My advice to new biomeds includes being ever present, available, and courageous. Be open to new opportunities. Accompany more-ex-
perienced team members on service calls, especially when support is related to advanced devices. Continually ask managers and supervisors for new opportunities. Absorb every bit of knowledge and experience so that you are better prepared for tomorrow’s opportunities, and boldly go.
BOYLAND: Develop mentor relationships with seasoned professionals who can help facilitate on-the-job training. Seek involvement in your local biomedical association.
4. WHAT SHOULD A HEALTH CARE FACILITY LOOK FOR WHEN IT COMES TO USING A THIRD PARTY FOR MEDICAL EQUIPMENT REPAIR AND MAINTENANCE?
LUCIDI: There are several important factors to consider when using a third-party. First and foremost, in today’s environment and at a minimum, only seek out service partners who operate within an ISO 134585:2016 certified Quality Management System (QMS). This shows a dedication to continued improvement and should provide clients with an increased level of trust. Second, seek out partners with longevity, and avoid the lure of those offering quick fixes and low-cost solutions. There are reasons why companies with over 20-30 years in the industry are still in business.
They’ve stood the test of time, weathered the storms, and have proven their commitment to their customers. Finally, seek out partners who specialize in key product lines versus those that are generalists across many device types. Although convenient, their experience and capabilities may not approach those with detailed expertise.
BOYLAND: Proven history and track record. Ask for a list of referrals.
5. IS IT POSSIBLE TO USE A THIRD-PARTY PROVIDER TO WORK WITH (ALONGSIDE) AN IN-HOUSE BIOMED TEAM FOR COMPREHENSIVE MAINTENANCE AND REPAIR?
LUCIDI : Currently, this scenario is very prevalent in the HTM industry. With the mass-shortage of HTM professionals, health care organizations are having to be creative to meet their objectives. One method is complimenting in-house teams with outsourced partners. Whether supporting specific device types, supporting remote sites, or assisting with routine preventive maintenance inspections, third parties and outsourced partners offer in-house teams a means of meeting their goals and commitments.
BOYLAND: Yes, but there is no one-size-fits-all solution. Quality resources and managing expectations between both sides is critical.
6. HOW DOES HTM TRAINING PROVIDE COST SAVINGS TO HEALTH CARE FACILITIES?
LUCIDI: One of the most effective means of reducing service spend is realized through employee investment. Benefits are twofold. First,
training HTM teams enables healthcare organizations to reduce their dependence on costly service contracts as well as time and material service costs. Research has shown that strategic investments in training, in-house HTM teams can be much more cost-effective than outsourcing or supporting through service contracts. Second, investing in HTM training demonstrates that the organization values its employees. In turn, employees realize greater job satisfaction and quicker advancement, and organizations experience lower employee turnover.
BOYLAND: A great way to lower the cost of maintaining equipment is to minimize expensive OEM service contracts. OEM training can be extremely costly, often underwhelming and isn’t always available. It’s not in the OEM’s best interest (for selling parts and contract) to have highly qualified biomed and third party imaging engineers. Quality, HTM service training can enable engineers to minimize contracts across a wide variety of imaging assets.
7. WHAT IS ONE THING YOU WISH SOMEONE HAD TOLD YOU WHEN YOU BEGAN YOUR CAREER IN HEALTHCARE TECHNOLOGY?
LUCIDI: Begin your continual education today, never stop learning, and never settle for the status quo.
BOYLAND: Get as much quality training as possible. Demonstrate a willingness to show your eagerness and prove the ROI on training.
TED LUCIDI Innovatus ImagingWe have now expanded our calibration service by adding locations in Virginia and Missouri.
Southeastern Biomedical is committed to providing convenient, cost effective onsite calibration and repair service of test, measurement, and diagnostic equipment operated by biomed departments in hospitals.
Our on-site test equipment calibration service will:
• Eliminate shipping costs and shipping damage
• Reduce downtime from weeks to hours
• Increase productivity
Our new high-end test devices provide us with a wide range of capabilities allowing us to:
• Calibrate and repair a wide variety of manufacturer’s test equipment
Our calibration management software will:
• Allow us to identify and notify you when your equipment is due for calibration
• Provide a history of calibration and repair services performed on your test equipment
• Provide online customer access to completed calibration certificates
All calibrations are traceable to the National Institute of Standards and Technology (N.I.S.T.)
•
We deliver an inside advantage you can’t get elsewhere:
Int er nal su ppl y c hai n su ppo rti n g hund re ds of ul tras ound pro b es a nd MRI c oil s
• Engi n eer in g ex pe r tise in cl ud es tra nsd u cer ar r ay s, pl as ti c m oldin g, 3 D pri n ti n g, ca bl e harne ss fabrica ti on , a nd pr ec ision len s es
• Repair proc e sses info rme d by ou r le gacy in FD A reg is tere d ma nuf act uri n g
MORE R EAS ONS THAN E VER T O EVER T O INSIST ON INNOVATUS IMAGING IN SIDE! Get the inside scoop at booth 400 at MDExpo this April
An online resource where medical equipment professionals can find all the information needed to help them be more successful! The easy to navigate Bulletin Board gives you access to informative blogs, expos and events, continuing education opportunities, and a job board. Visit www.MedWrench.com/BulletinBoard to find out more about this resource. Follow MedWrench at facebook.com/medwrench & linkedin.com/company/medwrench!
An online resource where medical equipment professionals can find all the information needed to help them be more successful! The easy to navigate Bulletin Board gives you access to informative blogs, expos and events, continuing education opportunities, and a job board. Visit www.MedWrench.com/BulletinBoard to find out more about this resource. Follow MedWrench on twitter @medwrench, facebook.com/medwrench & linkedin.com/company/medwrench!
Get ready for these events coming soon!
May 11-12, 2023
April17-21,2023
June 21-23, 2023
BLOG:
At MedWrench, our mission is to be the go to resource for the medical equipment industry. This starts with sharing tips with each other! Submit your tip today under the blog tab.
Ben Calibrating, Face of MedWrenchBLOG: Managing
In my defense, I have always refused to be a “yes man” and I had become accustomed to pushing back. Couple that with my personality (the way I come across) and I could relate with the results of the test. Together, I had a test that I completed and feedback from an associate that I respect, telling me the same thing basically. Knowing this, I began to focus on being easier to get along with and more collaborative with my peers. Not that I had not done this in the past, but there was still room for improvement.
BLOG: Mentoring
The field of biomedical engineering technology is a rapidly growing and constantly evolving field, with new technologies and advances emerging all the time. For individuals pursuing careers in this field, having a mentor can be an invaluable resource for professional and personal growth. In this article, we’ll explore the importance of mentoring in the field of biomedical engineering technology.
Visit MedWrench.com/Bulletin-Board/Continuing-Education for more details and to register for these upcoming classes.
BLOG:
Remote Power Tap (RPT) Part 2
Fast forward to November 2022, when our facility went through a mock-survey in preparation for our next inspection. The mock-inspectors cited three different issues regarding the use of RPTs. One of them was legitimate as the users had a table (not part of the assembly) plugged into an RPT that was attached to an IV pole. I would like to share the other two findings with you.
Principles of Servicing Nuclear Medicine Systems
March 27-31, 2023
Aquilion 16-Slice Training April 10-14, 2023
BMET to Imaging 2 April 17-28, 2023
Q: I have the configuration password; how do I change the default parameters? Do I need a specialized USB?
A: 3.13.3 Saving as User Configuration. You can change monitor settings as required and then save the changed settings into a user configuration. This patient monitor can save multiple user configurations, and you can name the saved user configurations.
1. Change monitor setting as required and make sure that the changes are suitable for your patient.
2. Select [Main Menu]l[Maintenance>>]l[User Maintenance >>]lenter the required passwordl[Manage Configuration >>].
3. Select [Save as User Default Config. >>].
4. Enter a name and select [Save]. If the entered name already exists, a message box will appear. Proceed by following the message. The configuration name saved in the patient monitor is in the form of “entered name+patient category+Config”. e.g., if you enter the name “ICU1” and the current patient is an adult, the configuration name will be “ICU1 Adult Config”.
Q:
During the overpressure verification test, the relief valve doesn’t open way past the max threshold of 325 mmHg for adult and only gets triggered at 335 mmHg. Same with neonate, doesn’t open at max threshold of 165 mmHg and only does at 180 mmHg. Is there a way to fix this?
A: I’m not sure, but if your pressure readings are accurate (PT1 and PT2 are reading correct values), I’d guess it’s the release valve not opening properly, but it could be the main board not signaling it on time. I could be wrong, but I’d try a new pnuematic kit first (especially if the unit is old) and then the main board.
A: Overpressure of PV-01 may occur if the source (upstream or downstream in the case of back flow) pressure exceeds PV-01 design pressure.
A: We have a lot of these (various ages) and as far as I know none have had this problem. Possibly your test equipment is not measuring properly if every unit you test is doing this. Are you testing according to the service manual or using a BP simulator/tester? Try verifying with another biomed’s pressure meter. Or have another biomed test to see if they get the same results.
is compiled from MedWrench.com. Go to MedWrench.com community forums to find out how you can join and be part of the discussion.
YP at MD is a group of young professionals in the HTM industry. Gather with your fellow up-and-coming colleagues at our MD Expos, HTM mixers and on social media to network, share ideas and discuss our bright future in the HTM industry!
LIVE:
MARCH 1 | Cognosos
Save the date for this live webinar. Participation is eligible for 1 CE credit from the ACI.
MARCH 8 | QRS & Datrend
Save the date for this live webinar. Participation is eligible for 1 CE credit from the ACI.
MARCH 15 | Phoenix Data
Save the date for this live webinar. Participation is eligible for 1 CE credit from the ACI.
MARCH 22 | Ordr
Save the date for this live webinar. Participation is eligible for 1 CE credit from the ACI.
MARCH 29 | BC Group
Save the date for this live webinar. Participation is eligible for 1 CE credit from the ACI.
All webinars and podcast are eligible for 1 CE credit from the ACI.
ON-DEMAND:
sponsored by Kontakt.io
“Veterans Affairs’ Path To Innovation With Kontakt.io RTLS Solutions”
sponsored by Sodexo
“Capital Equipment Planning in Challenging Financial Times”
sponsored by Pronk
“Defib Maintenance: Completing Manufacturer-based PMs Faster Than Ever Before”
sponsored by Ordr
“More Data More Problems – Data Reconciliation In The Modern HTM Environment”
PODCASTS:
sponsored by MMS
“The Hospitals of the Future”
“MedWrench is a website packed full of information you need to complete projects, purchase products and ensure correct processing and use of equipment.”
“MedWrench is a great resource for finding out about the newest advances in medical equipment and various sources that deal with med equipment repair and issues.”
“MedWrench is an online community of hospital machines for the
“I use the forums to search for error codes that may have happened to other biomeds.
“All in one website for those who want to continue learning about the different elements within the CE industry.”
“A great source for info and a good place to help others in need of expert advice.”
“A must have for any HTM professional.”
“A site focused on supporting the HTM professional, giving them instant access to industry experts to address topics and equipment relative to their day-to-day functions.”
- Julie Gottlieb, Account Manager Intl
- Ted Lucidi, Customer Experience & Clinical Insights
- Scott Williams, BMET Il- Amanda Vanderhoof, BMET Il
cool nerds.”
- Jina Walls, MedWrench Guru- Una Hamer,
Sterile Processing Supervisor
- Ed Bican, Lead Tech
is a product focused support network where medical professionals, purchasing administrators, manufacturers, dealers and industry experts can provide opinions, share ideas, and gather relevant information on medical technology and equipment. We want to say thank you for all of our users over the years. MedWrench wouldn’t be here if it wasn’t for our users!